Sheet Metal Roll Forming Machines
Metal roll forming systems are essential in the modern manufacturing industry, offering continuous bending of metal sheets into desired cross-sections. These systems are highly automated, cost efficient, and capable of producing complex profiles with exceptional consistency. The process involves feeding sheet metal through a series of roller dies, each performing incremental shaping until the final profile is formed.
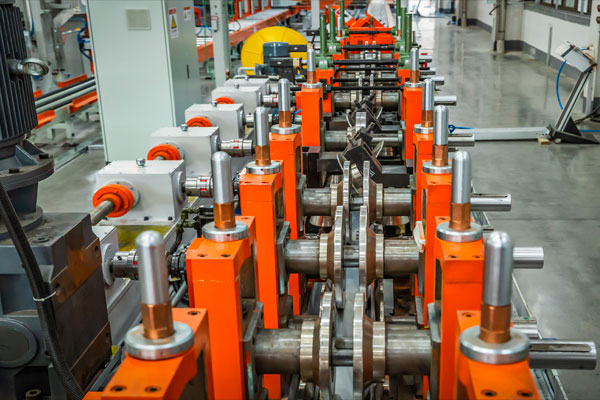
How Sheet Metal Roll Forming Machines
Sheet metal roll forming machines operate by gradually shaping metal coils into predefined forms through consecutive forming stations. These stations use precision rollers to apply consistent pressure, ensuring tight tolerances and smooth finishes. The machines can handle various metals, such as galvanized steel, aluminum, and stainless steel, making them versatile for numerous applications in construction, automotive, and industrial sectors.
Advantages of Roll Forming Systems
Roll forming systems offer several benefits over traditional metal forming techniques. They are capable of high speed production, low material waste, and minimal labor intervention. Because the process is continuous, it supports long production runs with uniform quality. Additionally, roll forming systems are energy efficient and support integration with punching, cutting, and embossing units for more complex outputs.
Applications Across Industries
Metal roll forming machines are widely used in industries such as construction (roofing sheets, wall panels, steel framing), transportation (truck parts, guardrails), and energy (solar panel supports, cable trays). The adaptability of roll forming systems allows for the customization of profiles to meet precise structural and functional specifications for each sector.
Metal Roll Forming Machine
A typical metal roll forming machine includes a decoiler, feeding system, forming mill (roll stations), cutting unit, and control system. The forming mill is the heart of the system, where the actual profile shaping occurs. Advanced machines are equipped with computerized controls (PLC systems) to ensure precision, repeatability, and easy parameter adjustments during operation.
Maintenance and Durability Considerations
Proper maintenance of roll forming machines is essential for long-term performance and product quality. Routine checks on rollers, lubrication systems, and cutting blades can prevent downtime and extend machine life. With durable construction and robust components, modern sheet metal roll forming machines are designed for years of intensive industrial use with minimal service interruptions.
Future Trends in Roll Forming Technology
The future of roll forming technology lies in automation, digitization, and sustainable manufacturing. Integration with smart sensors, real-time quality monitoring, and AI-based production optimization are on the rise. Moreover, advancements in energy efficient motors and eco friendly material handling reflect the industry’s move toward greener manufacturing using metal roll forming systems.