Product description
Features & Advantages
- Millimeter-precision production of Unistrut profiles, ideal for industrial and construction projects.
- Capability to form steel sheets with maximum allowable thickness and precisely folded edges for enhanced safety.
- Full compatibility with standard Unistrut fittings and accessories for quick and easy installation.
- High mechanical strength against bending and twisting, making it ideal for supporting pipes, cables, and solar panel structures.
- High production speed & continuous operation, perfect for large-scale projects.
This machine is the ideal choice for factories and workshops seeking cost-effective, fast, and high-quality production of Unistrut profiles for MEP systems and solar energy structures.
By implementing this technology, you can significantly reduce installation costs, minimize material waste, and maximize project efficiency.
Applications
MEP Support Systems
In industrial and construction projects, Unistrut channels are used as the main structural element for supporting pipes, cables, and mechanical equipment.
Profiles produced by the LOTOS Unistrut Channel Roll Forming Machine offer extended service life and help reduce maintenance costs.
Solar Mounting Structures
In solar power plants, profile strength and accuracy are critical.
Unistrut channels produced by this machine provide high load-bearing capacity and resistance to environmental conditions, making them the best choice for mounting and supporting solar panels.
Strut Channel Machine
The Unistrut Profile Roll Forming Machine is capable of producing four different profile sizes: 41×21 mm, 41×41 mm, 41×52 mm, and 41×62 mm. Among these, the 41×41 mm profile is the most common and widely used size, especially in solar structure frameworks. The other sizes are primarily utilized for mechanical support systems and lightweight building structures, such as substructures for false ceilings and space partitioning within buildings.
This machine can process steel sheets with thicknesses ranging from 1.5 mm to 2.5 mm, providing high versatility to meet diverse industrial and construction requirements.
Machine Components :
This production line features a comprehensive set of advanced equipment designed to ensure precise and efficient operation. The main components of the machine include:
- Hydraulic Decoiler: Smooth and controlled unwinding and feeding of steel sheets.
- Shovel Feeder: Accurate transfer of sheets to subsequent production stages.
- Leveling Unit: Flattening and leveling the sheets before entering the roll forming process.
- Pre-Shearing and Welding: Initial cutting and joining operations to prepare sheets for forming.
- Servo Feeding System: High-precision feeding mechanism for adjusting profile speed and length.
- Punch System: Creating holes and custom shapes on the sheets according to design specifications.
- Roll Forming Machine Section: The core part of the line responsible for the final shaping of profiles.
- Servo Tracking Cutting Die: Automatic, precise cutting of profiles to the specified lengths.
- Electric Control Cabinet: Complete control over machine operation and production line safety.
- Hydraulic Pump Station: Provides hydraulic power for related components and operations.
This comprehensive equipment integration significantly enhances production accuracy, speed, and quality, offering a highly automated solution to meet diverse industrial and manufacturing needs.
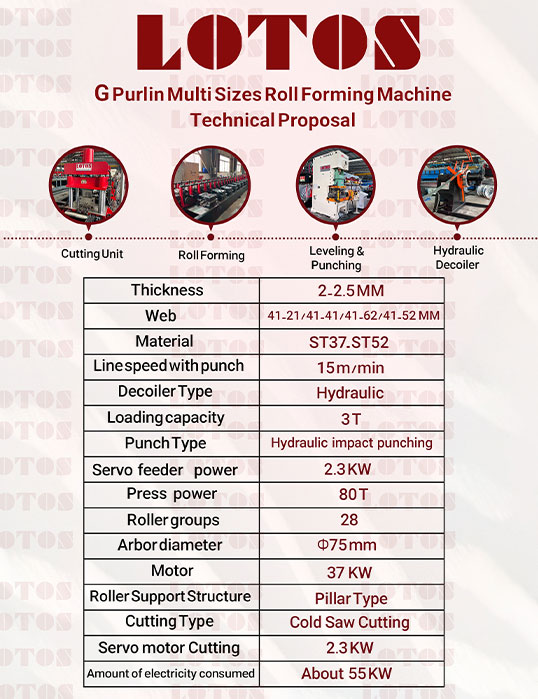
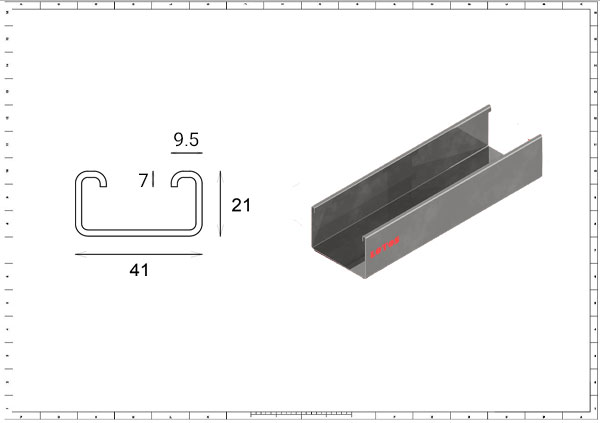
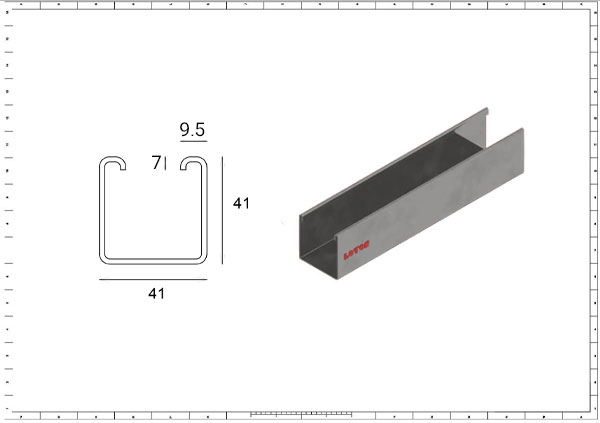
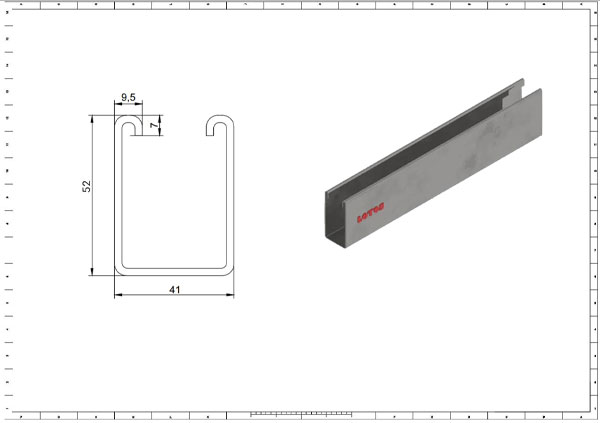
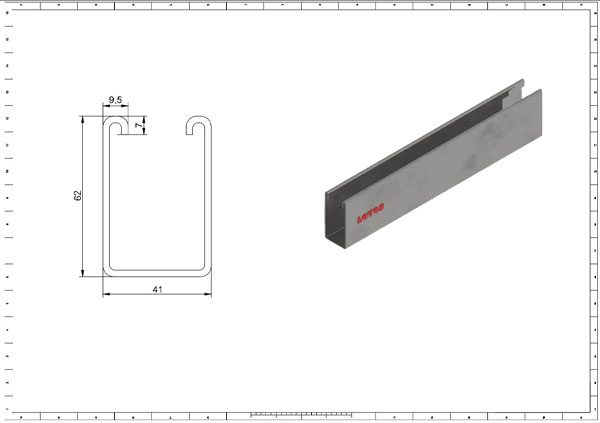
Thank you for staying with us! The Strut Channel Roll Forming Machine, with its high precision and quality, offers an ideal solution for producing standard and durable profiles across various industries including construction, plumbing, and renewable energy. If you’re looking to boost efficiency, reduce costs, and ensure product quality, this machine is your best choice.
Don’t forget to subscribe to our YouTube channel for more educational videos and detailed introductions to the latest technologies and applications of this machine.
For more information, technical consultation, and pricing inquiries, please contact our expert team. We are always ready to assist you on your path to manufacturing success.