Roll Forming Die and Processes: Roller Dies are the important parts of roll forming machine equipment.
The steps of the roller die process include:
Firstly, cutting raw material in length and preparing for the first step of machining.
secondly, lathe machining for the roller.
3: roller process is heat treatment.
4: surface grinding machine.
5: horizontal internal grinding machine
6: final CNC lathe machining.
7: chrome coating
Roll Forming Die and Processes
Roller Die + Forming
[embedyt] https://www.youtube.com/watch?v=AJOTYzOROxE[/embedyt]
in fact, LOTOS has enough experience in Roll Forming Die and Processes and manufacture to provide customers with quality, and durability, and cost-effective roll forming tooling.
Raw Material Roller Die
so,There are Raw materials for machining and fabrication in various sizes and shapes. if raw material dimensions don’t conform to necessary workpiece dimensions, need some type of cutting work to produce a workpiece.
Lathe Machining for roller
A lathe is a machining tool that uses for shaping metal. It works by rotating the workpiece around a STATIC cutting tool. The main use is to lift unwanted parts of the material.
- What Are the Common Types of Lathes?
- Speed lathe machine
- Capstan and turret lathe machine
- Bench lathe machine
- Automatic lathe machine
- Special lathe machine
- CNC lathe machine
Heat treatment roller process
Heat treatment is a group of industrial, and thermal, and metalworking processes used to alter the physical, and sometimes chemical, properties of a material. To remove stress, make the metal softer, refine the structure, or change its ductility.
Surface Grinding Machine
Likewise,A surface grinder is a machine tool used to provide precision surfaces and a smooth finish on flat surfaces. cuts chips of metallic or nonmetallic substance from a workpiece, making a face of it flat.
Chrome coating DIE roller
however, Chrome plating is a technique of electroplating a thin layer of chromium on a metal. The chromed layer can provide corrosion resistance, ease cleaning procedures, or increase surface hardness.
Step 5
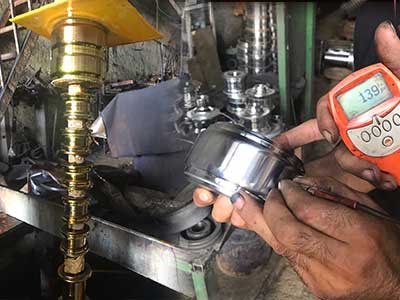